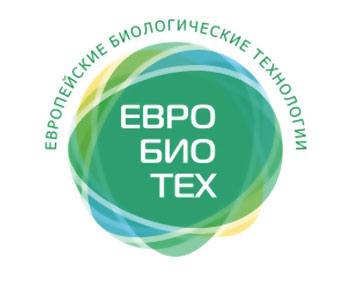
Ensuring food security of the region is one of the top-priority tasks for the development of the agroindustrial complex of the Samara region.
Upon initiative of the Government of the Samara region, the Corporation is implementing the investment project on construction of poultry production and poultry processing complex which will cover the requirements of the governorate’s residents in high-quality poultry meat and processed products. This project is of strategic importance because now about 60% of poultry meat is brought to the Samara region from other constituent entities of the Russian Federation and from abroad. Direct implementation of the project is carried out by subsidiary company of the Corporation – “Evropeiskie biologicheskie tehnologii”LLC.
Structure of poultry complex
Feed milling plant
Capacity of a plant is 30 tons of pelleted feed per hour. The plant will be fitted with the equipment of Russian company “Tehneks” based on the component parts from Italy and Germany. In the complex’s structure there is a unit for production full fat soybeans with the capacity of 6 tons per hour based on expanders from the company Almex (the Netherlands).
Elevator
Elevator complex for 77 000 tons of simultaneous grain storage will be equipped with the modern Danish driers and will ensure continuous operation of the feed milling plant.
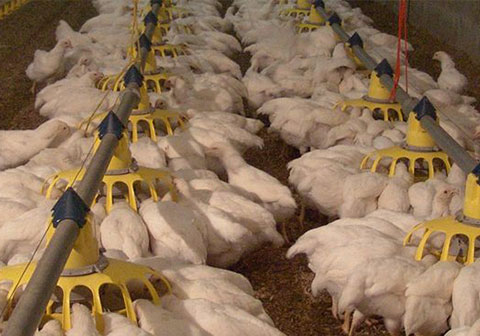
Premises for replacement chicks rearing
The project envisages construction of 12 premises (9 for female chicks and 3 for cockerels) which will be fitted with the equipment of company Vencomatic (the Netherlands). Total number of bird places is 183 000. The special feature of these premises is the system of cradles – plastic floors raised above the main floor. This system will allow not only to increase the useful capacity of the poultry house by 20-30 % but also will train birds to jump onto the perches using their natural potential from the very beginning.
Premises for holding parent stock
33 premises are connected by galleries for automated egg collection. Such system totally excludes the people’s contact with eggs and allows making sorting, marking and eggs laying to hatching trays fully automated. As a result eggs are loaded to the setters without any additional re-laying.
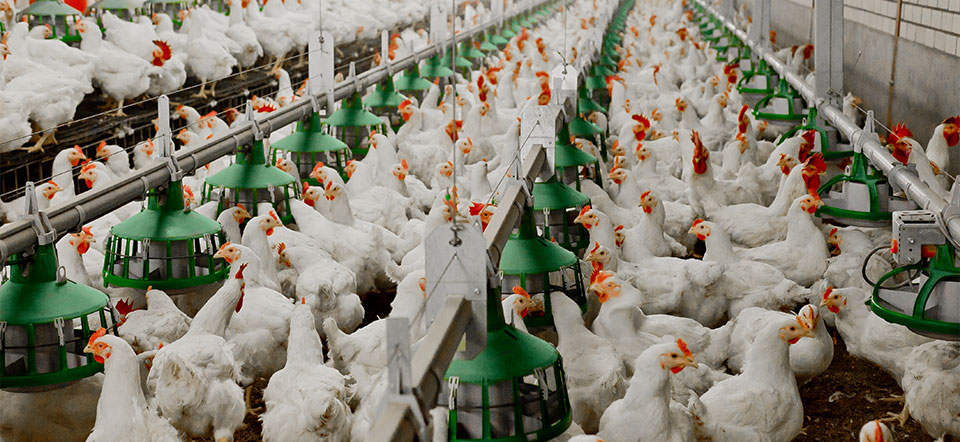
Premises for broiler fattening
It is designed to build 108 premises for broilers fattening (6 grounds with 18 premises each). It is planned to hold simultaneously more than 4.3 million broilers at the poultry complex. Exclusive building structure (rectangle made of enclosing structures – sandwich panels inside the load-carrying frame) was developed with the participation of company Vencomatic (the Netherlands) which is the absolute leader in the world poultry industry. Heat recuperation, Padcooling system and appropriate ventilation system enable to achieve the ideal microclimate in the poultry house.
Hatcher
Hatcher with a capacity of 52.7 million eggs per year will be fitted with the equipment of company HatchTech (the Netherlands) - the global leader of the industry - which implemented all its latest solutions in this project:
- Ventilation system of setters and hatchers that ensures totally laminar filtered air flow;
- Ultrasonic system for humidifying air in setters and hatchers;
- Special van HatchTravel for transportation of a day-old and 4 day- old chickens with keeping the necessary microclimate;
- 16 modules for 4-day nursing - breakthrough technology from the company HatchTech specially developed for controlling the environment during the first day of chicken’s life. After hatching, a day-old chicken is placed in the unit where the external factors (temperature and air velocity, relative humidity and carbon dioxide level, lightning) are continuously controlled and regulated so that to ensure the preservation of the optimum temperature of chickens’ bodies. All chickens have an easy access to the fresh air, water and food. In these ideal conditions chickens start to eat and drink immediately which results in better indicators of chickens’ safety.
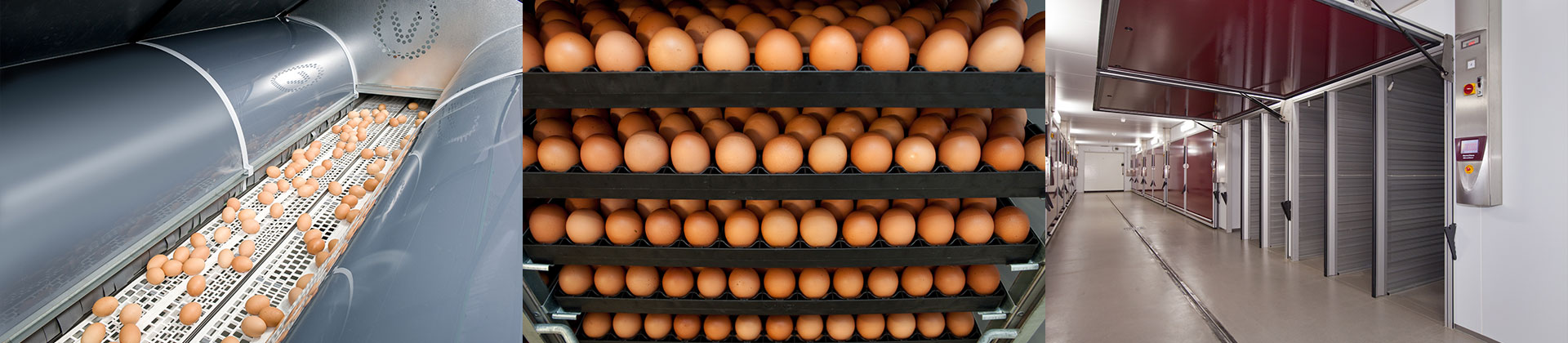
Slaughtering and poultry meat processing shop
Capacity of the plant will be up to 10.5 thousand boilers per hour. The plant will include fully automated lines for slaughter, gutting and anatomical poultry cutting. Shop of deep processing will allow producing the wide variety of semi-finished products, sausages and gourmet items. The plant will be equipped with modern systems of chilling and freezing.
work
places
Auxiliary facilities
- Grounds for transport washing;
- Grounds for water treatment;
- Grounds for manure storages;
- Grounds for storages of poultry house litter;
- Road maintenance facilities.
Engineering infrastructure
Poultry complex is a huge enterprise with large and difficult infrastructure. Thus, for example, the total water consumption will be more than 6 thousand cubic meters per day, there will be built around 30 distribution and transformer electric substations, gas-distribution station; new automobile roads with the junction to the route “Ural” will be laid and a railway-crossing of railway branch Krotovka-Sernovodsk will be reconstructed and reequipped.
The volume of industrial and utility effluents which will come to purification facilities will be equal to 3.5 thousand cubic meters per day. The task to bring the quality of the effluents to the fish conservation requirements will be solved in several stages at the local purification facilities made by company Nijhuis (the Netherlands); these stages include mechanical, chemical and biological processes and are completed by fine purification using sand and coal filters and UV disinfection.